Hydraulic Three-way Shuttle valve is a pressure controlled valve that shifts between a normal system inlet and secondary or emergency inlet. They are used for many applications in hydraulics including switching between alternate, standby, or emergency control lines, directing fluid to a brake cylinder for a winch, and providing sensitive steering controls in off-highway vehicles.
Typically, a shuttle valve has three ports; one normal system inlet port, a secondary or emergency inlet port, and an outlet port. The housing contains a sliding part called the shuttle that seals off either or both of the inlet ports.
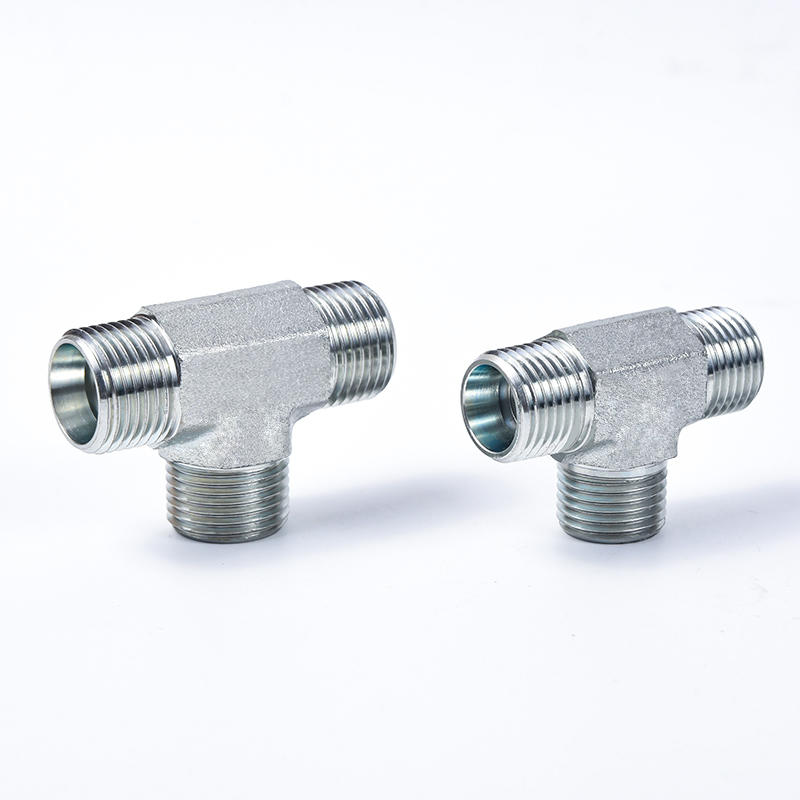
When a pump is running, fluid flows from the inlet port to the valve, through the valve, and out to the outlet port. When the pump stops, a spring arrangement in the shuttle shifts it back to the original position. It takes approximately 800 psi to shift it, allowing fluid to flow into the manifold and blocking the return port back to the pump.
A shuttle valve is a simple tube with three openings, one on each end and a middle opening. Inside each of the tube’s openings is a ball or other blocker.
When a fluid enters the tube, it pushes the ball towards the end that has a lower pressure. The ball then blocks the end with higher pressure and allows fluid to pass through that port, thereby linking both inlet ports and preventing the fluid from flowing backwards. This is an important feature that distinguishes a shuttle valve from a check valve placed back-to-back in dead-ended circuits, such as pilot and brake circuits.