Hydraulic check valves play a crucial role in safeguarding hydraulic systems from reverse flow, also known as backflow or backpressure. These valves are designed to permit fluid flow in one direction while preventing or restricting flow in the opposite direction. Here's how hydraulic check valves work to protect hydraulic systems:
Unidirectional Flow:
Hydraulic check valves are typically designed to allow fluid to flow in one direction only. This unidirectional flow feature is essential for preventing reverse flow and maintaining the intended direction of fluid movement within the hydraulic system.
Valve Types:
There are various types of hydraulic check valves, including ball check valves, poppet check valves, and pilot-operated check valves. Each type has its own design and mechanism for preventing reverse flow.
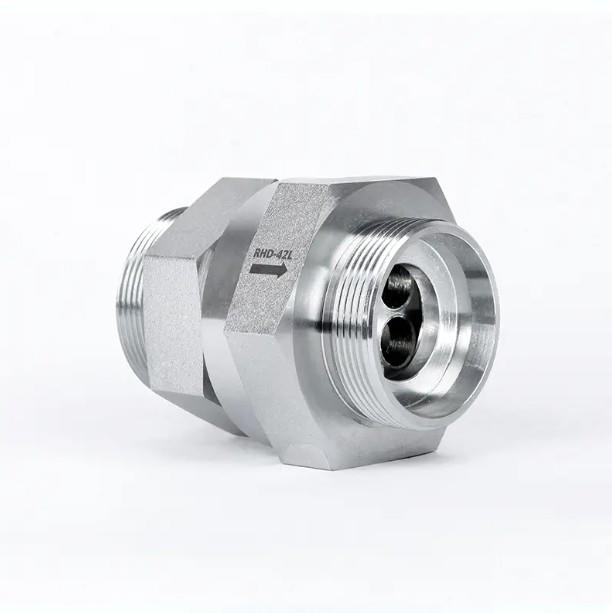
Spring-Loaded Mechanism:
In many hydraulic check valves, a spring-loaded mechanism is used to ensure the valve remains closed in the absence of forward flow pressure. The spring applies force to keep the valve in the closed position, preventing fluid from flowing in the reverse direction.
Cracking Pressure:
Hydraulic check valves have a specific cracking pressure, which is the minimum pressure required to open the valve and allow fluid to flow in the intended direction. Below this pressure, the valve remains closed, preventing backflow.
Pressure Drop and Leakage Prevention:
The design of hydraulic check valves minimizes pressure drop in the forward flow direction, ensuring that the hydraulic system operates efficiently. Additionally, the valve design aims to minimize internal leakage, further preventing reverse flow.
Application-Specific Designs:
Hydraulic check valves are designed to meet the specific needs of different hydraulic systems. For example, in low-pressure applications, simple ball check valves may suffice, while high-pressure systems may require more complex designs like pilot-operated check valves.
Preventing Cylinder Drift:
In hydraulic systems that use cylinders, a check valve can prevent cylinder drift. Cylinder drift occurs when the load on the cylinder causes it to move unintentionally due to gravity or external forces. The check valve prevents this movement by locking the cylinder in place when the directional control valve is in the neutral position.
Maintenance of System Integrity:
By preventing reverse flow, hydraulic check valves help maintain the integrity of the hydraulic system. Unwanted reverse flow could lead to pressure spikes, cavitation, or damage to components, and the check valve serves as a protective measure against these issues.
In summary, hydraulic check valves are crucial components in hydraulic systems, providing a unidirectional flow path and preventing reverse flow. Their design, including the use of springs and specific cracking pressures, ensures that hydraulic systems operate safely and efficiently.